Awesome Info About What Is The Purpose Of Torque Check
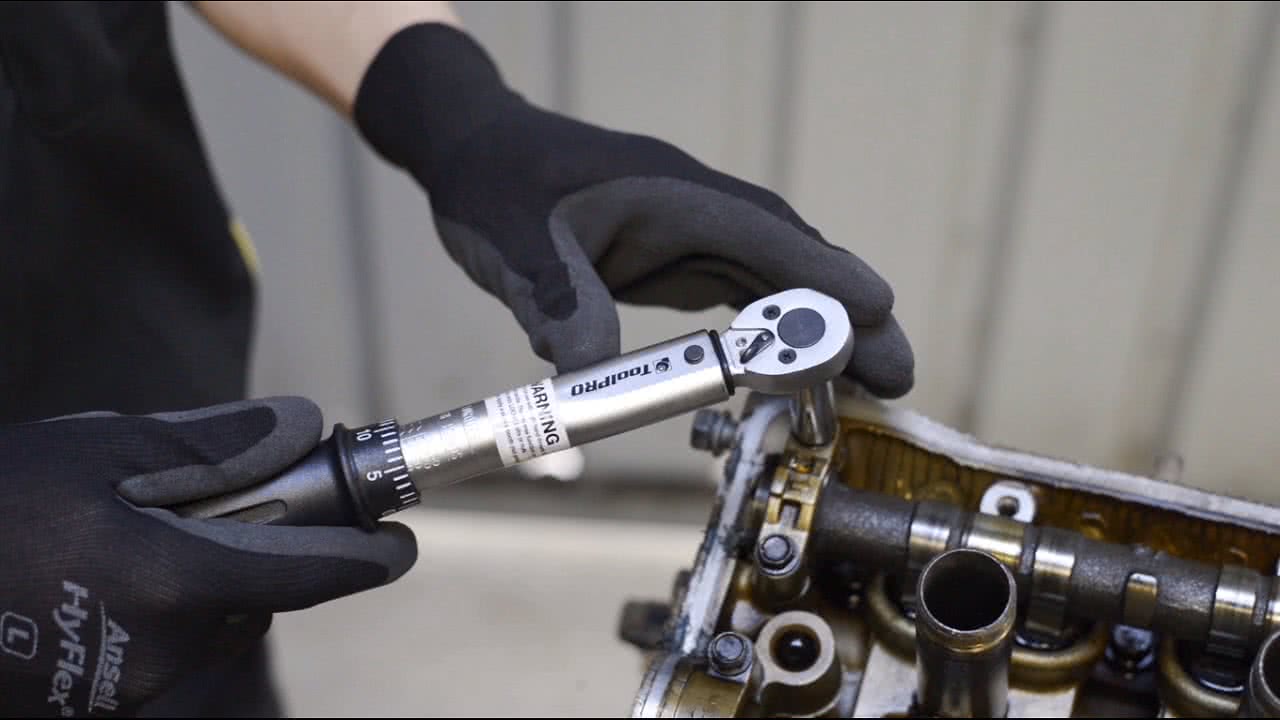
How To Choose And Use A Torque Wrench
Unlocking the Mystery
1. The Crucial Role of Proper Tightening
Ever wondered why mechanics and engineers are so obsessed with tightening things "just right"? It's not some weird compulsion, I promise! It all boils down to something called torque. Torque, in simple terms, is a twisting force that causes rotation. When you tighten a bolt or nut, you're applying torque. But applying the right amount of torque? That's where the magic, and the torque check, happens.
Imagine building a Lego castle. If you don't snap the bricks together firmly enough, your majestic creation is going to crumble at the slightest sneeze. Similarly, if you over-tighten them, you might crack the plastic. Bolts and nuts are kind of like Lego bricks for grown-ups, and torque is the glue (or, more accurately, the force) that holds them together. Too little, and things come loose. Too much, and you risk damaging the fastener or the parts it's connecting.
A torque check is essentially a verification process. It's the act of making sure that a fastener has been tightened to the precise torque specification recommended by the manufacturer. Think of it like double-checking your lottery ticket numbers—you want to be absolutely sure you've got it right!
Now, why is this so important? Well, let's just say that the consequences of getting it wrong can range from mildly annoying to downright catastrophic. We're talking about things like wheels falling off cars, airplanes malfunctioning, and even bridges collapsing. Okay, maybe that last one is a bit dramatic in most cases, but you get the picture: proper torque is serious business.
The Nitty-Gritty (but Not Too Nitty-Gritty!) on Torque Check Benefits
2. Beyond Avoiding Disaster
Okay, so we've established that torque checks help prevent things from falling apart (literally). But the benefits extend far beyond just preventing disaster. Proper torque also contributes to increased safety, reliability, and overall performance of whatever system you're working on. It's like giving your car (or your Lego castle) a longer, happier life.
Think about it: a properly torqued bolt experiences consistent tension. This means it's less likely to loosen over time due to vibration or thermal expansion. This reduces the need for frequent maintenance and repairs, saving you time and money in the long run. Who doesn't like saving money? I certainly do! My wallet thanks me every time.
Furthermore, consistent torque distribution ensures that the load is evenly spread across the connected components. This prevents stress concentrations, which can lead to premature failure. In other words, it keeps everything working harmoniously, like a well-oiled machine (pun intended!). Imagine a group project where everyone does their fair share that's what proper torque achieves for mechanical systems.
And let's not forget about accuracy! Using a calibrated torque wrench during a torque check guarantees a level of precision that simply can't be achieved by guesswork or "feel." It's the difference between baking a cake using a precise recipe and throwing ingredients together hoping for the best. One method is far more likely to result in a delicious outcome (and in the case of torque, a safe and reliable one).

Electric Motors Power And Torque Vs. Speed At Fernando Ward Blog
Torque Check
3. Torque Check Defined
Let's dissect "torque check" for a moment. "Torque," in this context, is a noun — it's the twisting force. "Check" is also a noun here, referring to an inspection or verification. So, "torque check" is a compound noun. It names a specific procedure.
The noun form is crucial. It indicates that its not just about torquing (a verb) or being torque-y (not a word, but you get the idea!). Its about a torque check — a specific, definable action with a purpose.
Because "torque check" is a noun, it acts as the subject of many sentences related to this process. For example, "The torque check is crucial for safety." Or, " Torque checks should be performed regularly." This highlights its importance as the focal point of the action.
Understanding its function as a noun helps us define its role and why it's so important. We are not focusing on "to check" or "checking" but rather on the process "torque check" and why we are doing the process.

How To Test A Torque Wrench? TorqueWrenchGuide
Tools of the Trade
4. Gearing Up for Success
So, you're convinced about the importance of torque checks. Great! But you can't just waltz in with a regular wrench and hope for the best. You need the right tools for the job. The star of the show, of course, is the torque wrench. This specialized wrench is designed to measure and apply a specific amount of torque to a fastener.
There are different types of torque wrenches available, each with its own pros and cons. Click-type torque wrenches are popular for their ease of use and audible "click" that signals when the desired torque has been reached. Beam-type torque wrenches are simpler and more affordable, but require a bit more skill to use accurately. Digital torque wrenches offer the highest level of precision and often feature built-in data logging capabilities. Choosing the right torque wrench depends on the specific application and your budget.
But it's not just about the wrench. You'll also need a set of sockets that fit the fasteners you're working with. Make sure to use high-quality sockets that won't slip or round off the corners of the bolts. And don't forget about calibration! Torque wrenches need to be calibrated regularly to ensure their accuracy. Think of it like tuning a musical instrument—if it's out of tune, the music won't sound right. Similarly, if your torque wrench is out of calibration, you won't be applying the correct torque.
Beyond the essential tools, having a good set of manuals and specifications is also crucial. These documents will tell you the correct torque values for each fastener in the system you're working on. Trying to guess the torque value is like trying to navigate without a map—you're likely to get lost (or, in this case, break something).
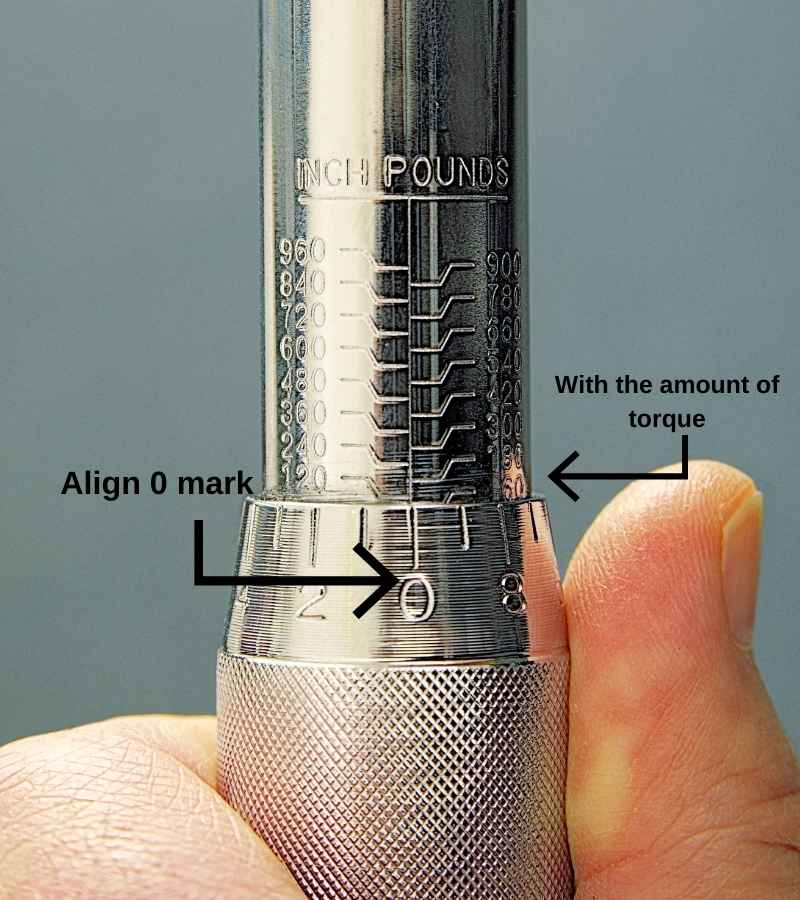
How To Use A Torque Wrench? (Working Principle & Types) Linquip
Real-World Examples
5. From Cars to Construction
You might be thinking, "Okay, this all sounds very technical. But where are torque checks actually used in the real world?" Well, the answer is: pretty much everywhere! From the cars we drive to the airplanes we fly in, torque checks are an essential part of ensuring safety and reliability.
In the automotive industry, torque checks are performed on everything from wheel lug nuts to engine head bolts. Properly torqued wheel lug nuts prevent wheels from coming loose, while properly torqued engine head bolts ensure a tight seal and prevent leaks. Mechanics use torque wrenches religiously to adhere to these specifications.
In the aerospace industry, the stakes are even higher. Torque checks are performed on every fastener in an aircraft, from the wings to the landing gear. A single loose bolt could have catastrophic consequences, so precision and accuracy are paramount. That's why aerospace technicians undergo extensive training and use specialized torque wrenches with incredibly tight tolerances.
Even in construction, torque checks play a vital role. When building bridges, skyscrapers, and other large structures, engineers specify precise torque values for the bolts that hold everything together. These torque checks ensure the structural integrity of the building and prevent collapses. So, next time you're driving across a bridge, you can thank a torque check for keeping you safe!
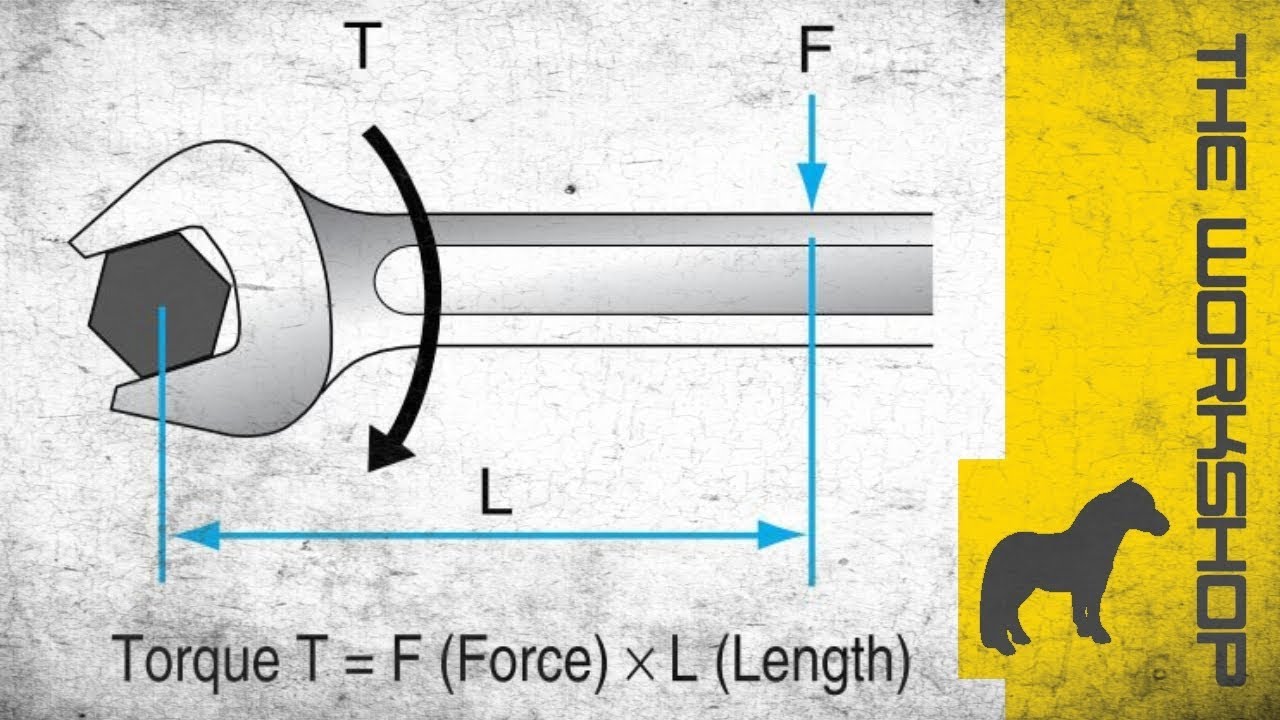
When Is Torque Zero
FAQ
6. Clearing Up the Confusion
Still have some questions about torque checks? No problem! Here are some of the most frequently asked questions, answered in plain English (no jargon allowed!).
Q: What happens if I overtighten a bolt?A: Overtightening can stretch the bolt beyond its elastic limit, causing it to weaken or even break. It can also damage the threads in the nut or the material being fastened. Think of it like bending a paperclip back and forth repeatedly—eventually, it's going to snap.
Q: How often should I calibrate my torque wrench?A: It depends on how often you use it. For professional use, it's generally recommended to calibrate your torque wrench every three to six months, or after a certain number of uses (check the manufacturer's recommendations). For occasional DIY use, you can probably get away with calibrating it once a year.
Q: Can I use a regular wrench instead of a torque wrench?A: While you can, it's strongly discouraged. A regular wrench doesn't allow you to accurately measure the torque being applied, which can lead to undertightening or overtightening. Using a torque wrench is like using a measuring cup when baking—it ensures you get the right proportions.
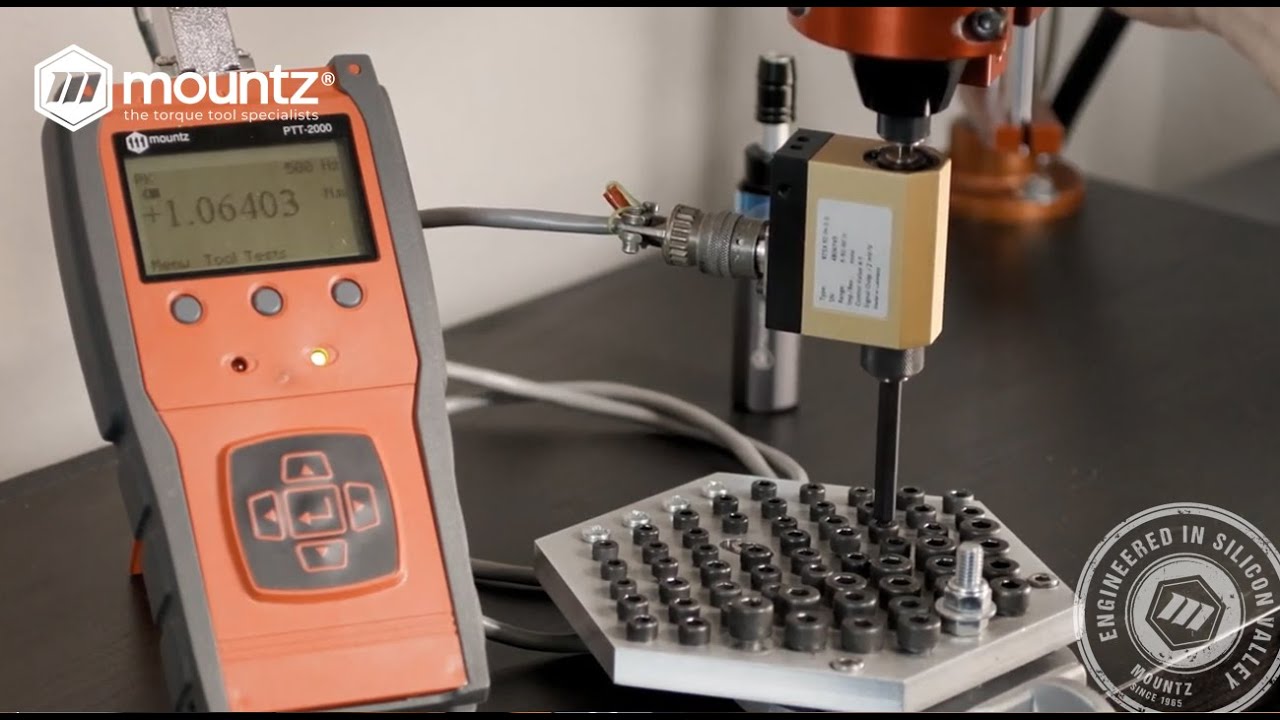